Foresight
Nov. 25, 2013
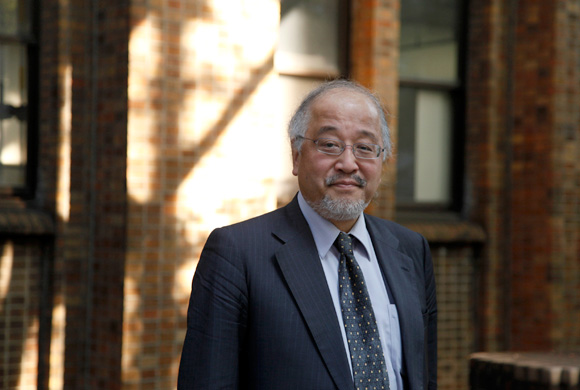
日本のものづくり停滞の根はどこにあるか
「経営的判断」が生んだイノベーションの足枷
[藤本隆宏]東京大学大学院経済学研究科 教授
日本のものづくりは世界的に見て、いま一体、どんな状況にあるのか。こういう問いは、つい大局的な経済の動向から語られがちですが、ものづくりは現場で起こっていますから、もっと足下の、現場の歴史をよく見ておく必要があります。経済・産業・企業・現場は、それぞれ連動しながらも、異なる動きをしますので、経済や産業といった大きな文脈だけを見ても、本質的な部分は見えてきません。
簡単に振り返ってみましょう。まず、戦後日本のものづくりの現場は、1950〜60年代の高度成長期に慢性的な労働力不足が発生し、いったん雇った人をずっと大事に雇用し続ける長期雇用が定着していったことで、特徴付けられてきました。会社の中で人を育て、その会社の産業のスペシャリストを養成していくかたちです。この結果、日本の製造業には、調整力の高い“サッカー型”の現場が多数発生しました。
日本の現場の強みは“サッカー型”のチームワーク
サッカー型の現場の持ち味は、「多能工のチームワーク」。長年の経験で自分の仕事以外の隣接したポジションの仕事についてもよく知っているため、互いにフォローし合うような組織となり、力を発揮します。アイコンタクト(暗黙知)によるパス回しの精度が向上していくイメージですね。
日本の現場が得意とするのは「調整集約型」の製品、言い換えると擦り合わせ型アーキテクチャを持つ製品です。現場で多能工たちが様々な擦り合わせを重ねることで、工程や品質が洗練され、製品クオリティが上がっていく。そういう日本らしいものづくりの土壌が培われていったわけです。
1970〜80年代になると、現場は「冷戦下における先進国間の国際競争」の時代を迎えました。この間、日本で貿易(特に輸出)に資する製品(貿易財)の現場は、円高と低成長による競争激化に対して、大いに危機感を持っていました。しかし、この状況に対応すべく、現場の能力構築を加速化したため、かえって国際競争力は増しました。ピンチを乗り越えたまさにこの時期、貿易黒字が定着し、貿易摩擦さえ起こしたわけです。
賃金水準がそんなに違わない先進国の間なら、現場の物的生産性が高ければ、即座にそれはコスト競争での勝利に繋がります。カンバン方式で知られるトヨタの方法論が「付加価値のよい流れ」として世界的に注目されたのも、この頃でした。
ところが、1990〜2000年代は状況が一転。「冷戦後における新興国を含むグローバル競争」の時代となり、日本の貿易財の現場が苦境に立つことになりました。とくに厳しくなったのは、設計面で比較優位を持たないモジュラー型(組み合わせ型)の製品を作っていた現場です。例えば、デジタル財の生産現場は、史上最大ともいえるハンディを背負って、大変苦しい状況に置かれることになります。
東西の冷戦が終わり「鉄のカーテン」が開くと、日本のすぐ西で賃金が日本の20分の1、人口が10倍という低賃金大国・中国が突如、世界市場に乗り込んできました。あまりに急で、日本は受け身がとれません。それでも多くの国内現場は、生産性を2倍、3倍、あるいは5倍以上にすることで対抗しました。これ自体、凄まじい粘りですが、結局、大企業の国内工場はかなりの数が閉鎖され、中小・中堅企業の倒産も出ました。とはいえ、全体として見れば、驚くほど多くの国内工場や中小企業が生き残ったといってよいでしょう。これはすごいことだと思います。逆境が強い現場を育てるのです。
そして2010年以降、日本の現場はリーマンショックや大震災、超円高などを経験してきて、相変わらず厳しい状況にあります。しかし、新興国の賃金高騰もあって、史上最悪のハンディを背負った苦難の時代は脱しつつあるといえます。厳しい競争環境でも生き残った国内の優良現場にとっては、長いトンネルを脱しつつある、あるいは「夜明け前」的な状況といえるのではないでしょうか。
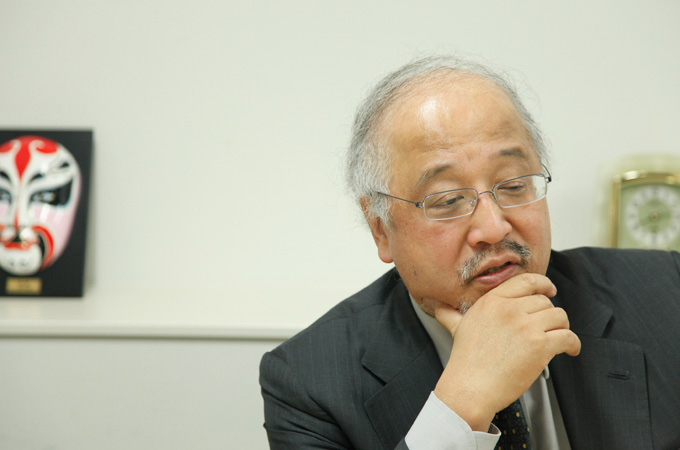
短期的な経営指標にとらわれて
生き残る現場を潰していないか
「夜明け前の闇は最も暗い」と言いますが、今、一番重要なことは、経営者やマネジメント層が国内外の現場の実力と潜在力を正確に理解すること。日本や新興国の現場における生産性や賃金の長期トレンドをしっかりと把握した上で、目先の状況に振り回されるのではなく、あくまでも「長期全体最適のグローバル経営」を目指すことです。
例えば、新興国との賃金差が縮小したことで、新興国の拠点でも現場の人員の定着率が下がり、人材の確保が容易でなくなる状況が生まれてきました。そんななか、国内拠点では生産性を上げる余地がまだ大きく残されていると判断できる場合もあります。
こんなとき、国内外での賃金差や円高といったハンデを生産性向上で跳ねかえしてきたのが日本の現場なわけですが、それを閉鎖してまで低賃金の海外拠点に全面的に生産移転をしようとするのは、論理的にも実践的にも誤りでしょう。しかし、こういう選択をしようとする経営者は、決して少なくありません。
これは、海外拠点における賃金の低さや、当期に発生した製造原価など、短期の数字だけしか見ず、「現場の実力」のような直接数値では図りづらい国内拠点の強さを過小評価していることが原因です。例えば、主力製品の主力ラインにおける作業時間あたりの付加価値額(付加価値作業時間比率)は国内と海外の拠点で比較してどうでしょう。生産性向上の実態は、両者で比較してどちらが優れているでしょうか。そういう比較を怠って直近の損益計算書だけで海外移転の判断を下した企業も多くいたのです。
現場の“質”を自分の目で確認しておらず、役員会の空気だけで国内現場の閉鎖を決定するような経営陣は、残れたはずの現場を潰してしまいます。それが結局、日本全体の生産性を落とし、次世代の生活水準に悪影響を与えることになるのです。それはいわば不戦敗です。経営ミスであり、人災とさえ言えます。
中小企業の「現場との距離感」を見習う
つまり、日本のものづくりがいま停滞しているというのであれば、その最大の原因は、大企業系の経営者にあるといえるでしょう。現場から遠い彼らマネジメント層の中には、日本経済の暗いニュースを日々受け取っているせいで、鬱的な気分から理論的にも実証的にも根拠の怪しい「製造業悲観論」や「全産業空洞化論」に振り回されてしまいがちな人達もいます。
マスコミなどの言説には、短期的なトレンドを過大評価した性急な論調も見かけますが、それらを鵜呑みにせず、自分の頭で論理的にものを考えることが大切です。そうしてグローバル長期全体最適の経営を目指していただきたいと思います。
現場に寄り添い、よく観察してものづくりに励めば、まだまだイノベーションのチャンスはいろいろなところで見つかると思います。こういう点では、中小企業の経営者に学ぶところも大きいと思います。大企業の経営者層は、良くも悪くも「資本市場に向き合っている」というプレッシャーが重いせいで、世界的なトレンドをウォッチすることに忙しく、現場を熟知していないことが多い。「教育担当」の肩書きを持つマネジメント層が、現場でどんな技術が継承されていて、どんな努力がなされているのかを知らないといったこともよく聞きます。
中小企業の社長室は、よく工場の2階とかにありますよね。彼らは毎日現場を目にし、変わったことがないか、改善の余地はないか、新しいアイデアを新しいビジネスに結びつけられないかと、自分の肌感覚で判断しています。とにかく生き残らなければ、自分が雇っている200人、300人がたちまち路頭に迷い、困窮してしまう。そんなリアリティもあるから、いつも必死にもがいています。そうしていると、ゴールが見えていなくても、いつの間にか事業機会という光がみえてくる場合もあるんです。
後編では、そのあたりの話から、大企業系の経営陣に求められていることについて考えてみたいと思います。
WEB限定コンテンツ
(2013.10.30 東京大学の研究室にて取材)

藤本隆宏(ふじもと・たかひろ)
1979年、東京大学経済学部経済学科を卒業し、1989年6月、ハーバード大学ビジネススクール博士課程修了。東京大学経済学部助教授、同 大学院経済学研究科助教授を経て、1998年より同教授。現場というミクロのレベルで、産業競争力を高める設計構想(アーキテクチャ)とものづくりの組織能力のあり方を実証的に研究している。